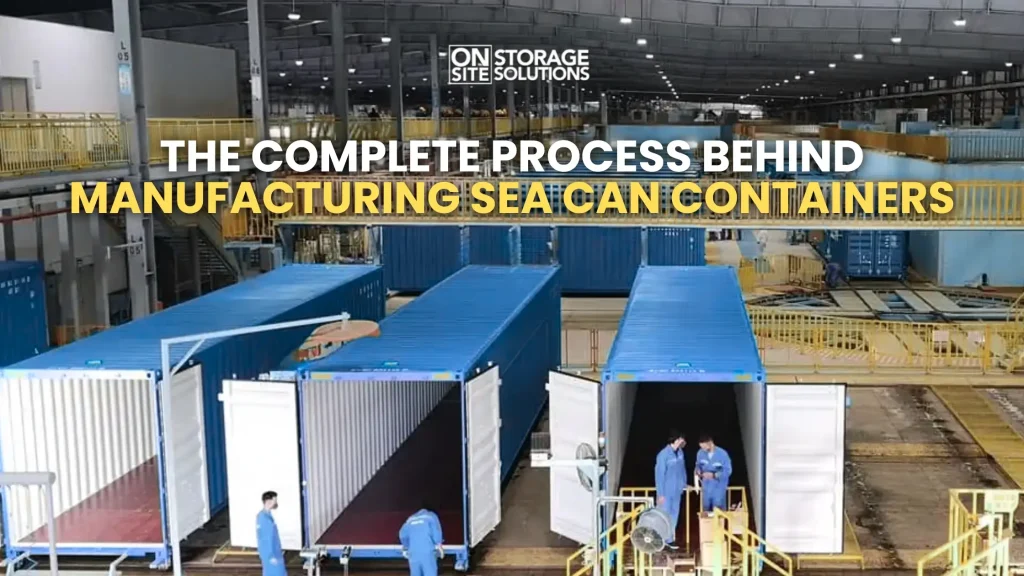
Sea can containers, the large metal boxes piled on ships, trains, and trucks, have become a vital part of global trade and transportation. Beyond their primary role in shipping, they’re increasingly being used for storage, housing, and even creative architectural projects. But have you ever wondered how these incredibly durable structures are made? Let’s delve into the fascinating shipping container manufacturing process.
History of Sea Can Containers
The modern sea can container was invented in the 1950s by American businessman Malcolm McLean. He created a standardized, reusable container to streamline cargo handling and make shipping more efficient. In 1956, his company, Sea-Land Service, launched the first containerized shipping service. By the early 1960s, the International Organization for Standardization (ISO) set universal container size standards, enabling global use.
Containerization revolutionized global trade in the 1970s and 1980s, reducing shipping costs and increasing speed. Today, containers are essential for transporting goods worldwide and are also repurposed for construction, housing, and other uses. The shipping container remains a key driver of globalization and modern logistics.
Step 1: Creating the Wall Panels
The initial step in how sea containers are made is the production of the wall panels. The process starts with giant rolls of steel, which are unrolled and cut into pre-measured sheets. These steel sheets are then sandblasted and primed to remove rust, dirt, and other contaminants.
This surface preparation is critical for ensuring the longevity of the container. The sheets then undergo corrugation, a process of folding the metal to create ridges and grooves. This corrugated steel design adds significant strength and rigidity to the panels, enabling them to withstand heavy loads and the rigors of shipping.
Once corrugated, the smaller sheets are welded together to form full-sized wall panels. Finally, square tubing is welded to the top and bottom of each panel, allowing them to be connected to the floors and roofs.
Step 2: Assembling the Floor Frame
The next phase is the assembly of the undercarriage or floor frame. This frame forms the foundation of the durable sea container. It consists of two long I-beams laid out parallel, running the length of the container. Smaller I-beams are then welded perpendicularly between the longer beams, forming a raft-like base.
The use of I-beams is vital as they provide excellent structural support and resistance against bending, enabling the shipping container floor to carry heavy cargo. Once complete, the floor frame is sanded down to ensure there are no rough joints. This step ensures a smooth surface for the next stages of construction and a robust base for the container.
Step 3: Constructing the Doors and Corner Posts
After the floor, it’s time to work on the doors and corner posts. Like the wall panels, shipping container doors are made of corrugated steel encased in square steel tubing. A rubber seal is then wrapped around the edges of the doors to ensure they are watertight.
The corner posts, also known as corner fittings, are essential for the structural integrity and stacking ability of the container. They are welded to the I-beams of the floor frame and are designed to bear the weight of multiple containers stacked above. The precise construction of these elements is crucial for safe and efficient handling.
Step 4: Assembling the Box
With all the main components ready, the assembly of the container can begin. The door assembly is first installed onto the floor frame, followed by the wall panels. These components are precisely positioned and welded in place.
Finally, the roof panel is lowered and welded to the top of the walls, thus enclosing the entire structure. This stage transforms the separate parts into the recognizable box shape of a sea can container.
Step 5: Priming and Painting
Once the box is assembled, it moves to the painting area. The first layer applied is a primer, which helps the subsequent paint layers adhere better to the steel and provides added protection. This undercoating is crucial for the long-term durability of the container.
After the primer dries, the container is spray-painted several times with special paint designed to withstand harsh marine environments. The multiple layers of paint create a protective barrier against rust, salt water, and other environmental elements, crucial for a durable sea container.
Step 6: Installing the Flooring
The next stage of the sea can container construction is flooring installation. Marine plywood panels are treated with a protective coating to prevent pest infiltration and water damage. The panels are placed inside the container and screwed down into the steel floor beams. This creates a durable and level surface that is ready for cargo.
Step 7: Applying Labels and Identification
Now, the container is ready for its unique markings. Shipping line logos, advertisements, and identification codes are applied to the container’s exterior. The container identification codes are critical for tracking and managing the containers globally.
Each container has a unique code with 11 alphanumeric characters; the first three letters identify the owner, the fourth identifies the product group (U, J, or Z for the container, attachable equipment, or trailer, respectively), the fifth through tenth are a serial number, and the final is a “check digit” to verify the preceding numbers.
Step 8: Adding Hardware, Locks and Sealant
The next step involves installing the door hardware, including handles and locking mechanisms. A rubber gasket is wrapped around the doors to ensure a watertight seal. Finally, a waterproof sealant is applied to the bottom of the container to prevent water intrusion. These final steps are critical to maintain the integrity of the container’s watertightness.
Step 9: Waterproofing and Testing
The final stage of the manufacturing process is a thorough waterproofing test. The container is soaked with water and then examined for any leaks or vulnerabilities. If it passes the test, the container is certified as complete and ready to be deployed. This rigorous testing ensures that the container can safely and securely transport cargo across oceans, making them reliable for their intended use.
Where Are Sea Can Containers Made?
The journey of a sea can container begins in massive industrial factories, primarily in China, which dominates global production. These facilities utilize heavy-duty machinery to cut, weld, and assemble containers on a large scale, with some manufacturers producing over 7,800 twenty-foot containers daily.
While various countries played a role in the early days of container manufacturing, China has become the central hub due to its vast manufacturing capabilities and extensive port infrastructure. Major Chinese manufacturers, such as China International Marine Containers (CIMC), Dong Fang International Containers, and CXIC Group, produce the majority of the world’s dry and refrigerated containers, fueling the global shipping industry.
Beyond Shipping: The Versatile Sea Can Container
While originally designed for shipping, sea can containers have found numerous other applications. They’re used for on-site storage, temporary offices, and even as building blocks for homes and commercial spaces. The inherent strength and durability of the sea can containers make them a cost-effective and versatile building material. The ability to modify them also means that they are suitable for a wide range of uses.
Conclusion
The manufacturing process of a sea can container is a complex operation that involves numerous steps, from the initial steel sheet to the final watertight, tested product. What is a sea can container? These containers are more than just steel boxes; they are the backbone of global trade and a testament to modern engineering and manufacturing. Their robust design and versatility make them suitable for a wide variety of applications beyond their initial use in shipping, making them valuable in many ways.
Looking for Sea Can Containers For Sale?
At On-Site Storage Solutions, we’re offering a wide range of high-quality shipping containers for sale, including 40 feet containers perfect for personal or business use.
We have the right option for storage containers for sale at residential and construction sites, among others. To buy a shipping or storage container, call us at (888) 977-9085 today! We’ll help you find the perfect storage solution to suit your needs.